The design and the construction of tools is specialized work which make it possible to produce precision components. These design and construction processes impact the quality of the product, the efficiency of production, and the cost. Every industry, from automotive to aerospace, relies on tools that are designed to work for them. Manufacturers with skills in tooling design are able to make functional and durable tools for diversified uses. At Allwell Cast, novel approaches develop dependable production systems for outstanding performance results.
The Essence and the Role of Tooling Design
The successful manufacturing of a product begins with the proper tooling design. It covers the engineering factors of creating tools, dies, molds, and fixtures required for the conversion of raw materials into accurate components. Effective tooling designs lead quality products to be manufactured, waste of materials to be reduced, and operational efficiency to be enhanced. Engineers take into account several aspects including material characteristics, production amounts, and limitations of the processes to be able to develop effective tooling systems. A faulty design can result in production anomalies and defects which translates to greater costs and lower product usage life.
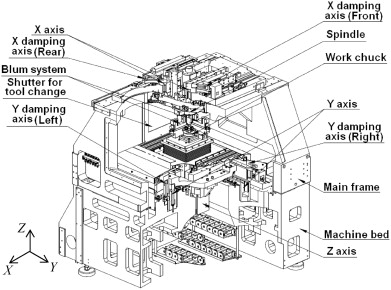
Important Aspects to Consider When Designing a Tooling
The success of a tooling designrelies on a material choice, geometry, and operational specifics. Engineers assess factors such as tool materials’ toughness, thermal expansion, and wear resistance to outline what tools will be made off. Geometric accuracy is crucial for the tool being produced as well as the quality and quantity of production. More intricate designs require more sophisticated CAD modeling that will aid in the conception and iteration of the model prior to making it. Also, the engineers need to consider operational specifics to improve the service life of the tool and optimize the production cycle.
New Methods for Designing a Tool
Contemporary tool design incorporates with it CNC machining, additive or 3D manufacturing, and high precision assembly. CNC machining allows for the production of tools with minimal inaccuracies, thus maintaining the efficiency of mass production. 3D printing has become known as a very simple method of rapid prototyping and design verification before final production. The methods of high precision assembly allow for all components to be incorporated without misalignment, therefore boosting the effectiveness of the equipment. Employing these methods allows customer satisfaction as manufacturers are able to create durable tools designed for high pressure applications.
Difficulties in Tooling Design and Construction
The design and construction of tooling has and continues to be a challenge regarding complexity. Material pricing continues to increase, and engineers are tasked with designing within the boundaries of reduced costs without sacrificing quality. Additionally, high production efforts and time are needed due to complex geometries that require advanced manufacturing processes. Therefore, deep tolerances can be very difficult to maintain with high strength materials. These hurdles can be overcome with new design approaches as well as improved production technologies.
Improving Productivity with Precision Tooling
Precision Tooling Systems claim increase in productivity while decreasing lead time and maximizing precision. Utilizing smart tooling systems with sensors for real-time monitoring allows for predicting maintenance and minimizing downtime. Tool life is further extended with the use of coatings and surface treatments; ensuring less wear and tear. Modular systems allow for greater flexibility to adjust with limited lead time to changes in production. All of these innovations provide greater productivity and cost efficiency for manufacturers.
Conclusion
Strategic tool design and careful toolmaking lead to successful production processes by allowing for high-quality workmanship with the least amount of waste. The engineer has to take into account the material choice, accuracy, and operational requirements of the system in order to design productive tooling systems. In today’s world, while a lot of progress has been made in machining, other industries are including efforts in additive manufacturing where optimizing tool construction processes for making strong and functional tools is a priority. The dynamism of industries dictates that tooling will need to continue to evolve indefinitely in order to keep up with exacting manufacturing requirements. Allwell Cast’s tooling experts are committed to exacting and highly productive precision castings to enable customers’ efficiencies.