Die casting maintains its status as one of the most effective processes for manufacturing complex and precise metal parts. The automotive, aerospace, and electronics industries are heavily dependent on die casting services to produce high-quality and long lasting components. The parts are produced with high dimensional accuracy and superior surface finishes using sophisticated technologies. At Allwell Cast, their die casting competence ensures that cost-effective components are produced that fulfill the stringent requirements of various industries.
Learning about the process of die casting
The die casting process includes injecting molten metal at high pressure into a reusable mold called a die. This method is effective in generating components with close tolerances while the machining operations are greatly reduced. Aluminum, zinc, and magnesium are widely used because of their superior strength-to-weight ratio. This process is ideal for mass customization and improves scalability. Engineers set other variables like temperature, pressure, and cooling rates to optimal values to improve product quality.
Methods of die casting
Hot Chamber Die Casting
Hot chamber die casting is appropriate for lower melting point metals such as zinc and magnesium. The metal is stored in a heated chamber, which enables fast injection cycles. This method reduces wastage of material and ensures quick production of parts.
Cold Chamber Die Casting
Cold chamber die casting operates well with low melting metals and hybrids. Liquid conditions of the metal is poured into the die before being injection, instead of using a hot chamber with auto molding. This procedure helps reduce wear on precision machine parts and maximizes machinability of the features.
Advantages of Die Casting Services
High Dimensional Accuracy
Very few secondary processes are required as die casting is capable of producing intricate components with very tight tolerances. All parts are interchangeable, even with mass production.
Enhanced Strength and Durability
Mechanical properties of die casted components are exceptional. Structure of the metal and its strength is enhanced due to high speed cooling, leading to greater durability and resistance to severe impacts.
Cost-Effective Mass Production
Die casting is unique in that it saves time when using large quantities due to low labor capital and loose material as well as saving on the usage of materials. Such practices make it incredibly economical when there is a high volume of production.
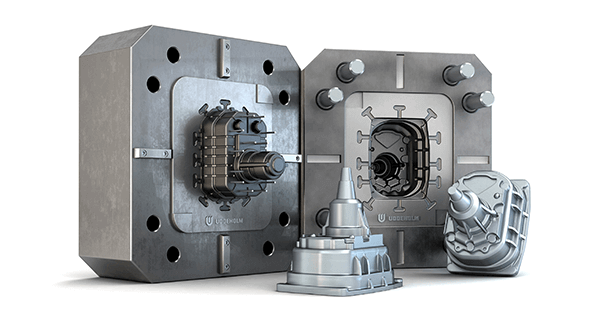
Material Selection for Die Casting
Selecting the most appropriate material is crucial, given the characteristics and intended use of die cast components.
Aluminum: Impervious to corrosion, light weight and a common material in the automotive and aerospace industry.
Zinc: Superior casting accuracy which is required for electric details and other delicate items.
Magnesium: High strength to weight ratio often used in housing for electronics and other structural information.
Quality Control in Die Casting Services
Advanced methods of testing and inspection for die cast components are important to maintaining quality in die casting services.
X-ray Inspection: Identifies internal defects such as porosity and cracks that threaten the overall integrity of the part.
Dimensional Analysis: Employs CMM tools to check for compliance and accuracy of the design details.
Surface Finishing: Processes such as shot blasting and anodizing enable increased corrosion protection and enhancement of beauty.
Uses of Die Casting in Different Sectors
- Die casting is beneficial to many industries because it is light, strong, and inexpensive.
- Automotive: Engine parts, transmission housings, and brackets are some structures that have benefited from die casting.
- Aerospace: The use of lightweight aluminum and magnesium castings improve fuel economy and strength of the aircraft components.
- Electronics: Heat resistant plastic casings and connectors improve quality in electrical and other consumer electronic devices.
Final Remarks
Thermal efficiency, precision, and affordability makes die casting solutions an ideal selection for manufacturing. Allwell Cast makes industry leading products because of their thorough knowledge in materials selection, process control, and quality assurance. As technology progresses, products manufactured using die casting become more efficient. Therefore, die casting remains the best choice for the extensive use in many industrial fields.